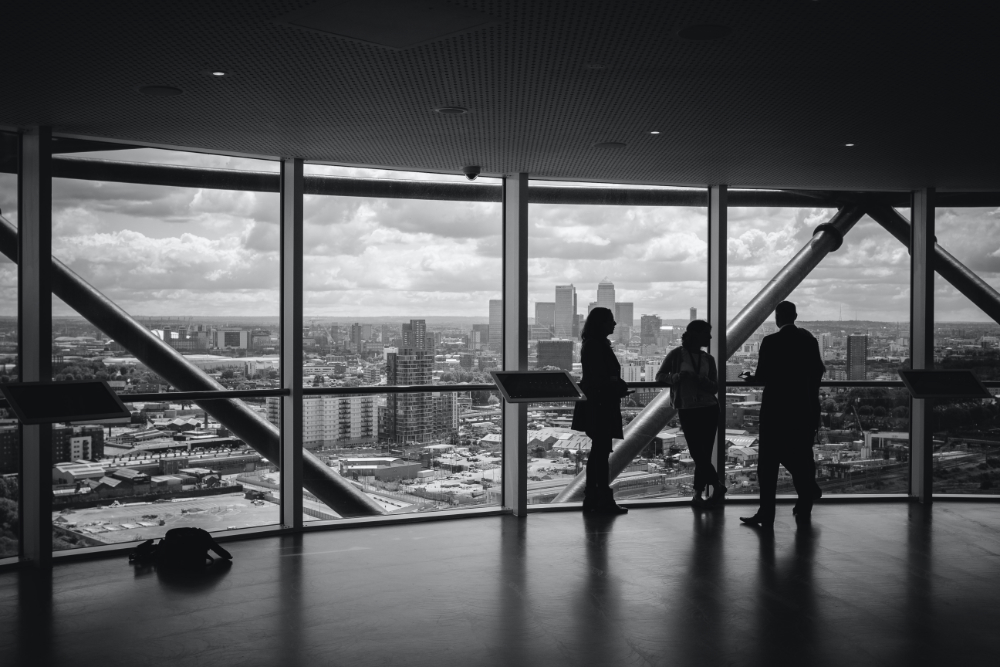
The Ultimate Guide to ISO 9001 Certification in Australia: Cost, Process and Benefits
What is ISO 9001?
ISO 9001 is an internationally recognized standard for Quality Management Systems (QMS) developed by the International Organization for Standardization (ISO). The standard provides a comprehensive framework for organizations of all sizes and industries to establish, implement, and maintain a QMS that ensures consistent delivery of high-quality products and services. Updated periodically to reflect the evolving business landscape, the most recent version of the standard is ISO 9001:2015. By focusing on customer satisfaction, risk management, and continuous improvement, ISO 9001 aims to help organizations optimize their operations, increase efficiency, and enhance overall performance.
The foundation of ISO 9001 is the set of seven quality management principles that guide organizations in developing and maintaining an effective QMS.
These principles include:
- Customer focus
- Leadership
- Engagement of people
- Process approach
- Improvement
- Evidence-based decision-making
- Relationship management
By incorporating these principles into their daily operations, organizations can create a culture of quality and excellence that spans across all aspects of their business. The ISO 9001 standard is designed to be flexible and adaptable, allowing organizations to tailor the QMS to their unique needs and objectives.
Obtaining ISO 9001 certification offers a wide range of benefits to organizations, including improved operational efficiency, enhanced customer satisfaction, and increased marketability. By implementing a QMS that meets the ISO 9001 requirements, companies can identify areas for improvement, reduce waste, and streamline their processes. Furthermore, the certification serves as a mark of credibility, demonstrating to clients, partners, and stakeholders that the organization is committed to maintaining a high level of quality in its products and services. This can lead to new business opportunities, better relationships with suppliers, and a competitive advantage in the marketplace. Overall, ISO 9001 certification helps organizations build a strong foundation for long-term success and growth.
The History of ISO 9001
The history of ISO 9001 dates back to the mid-20th century when the need for standardized quality management systems became apparent due to the rapid growth of international trade and technological advancements. The roots of the standard can be traced to the British Standards Institution’s BS 5750, which was developed in the late 1970s to address the need for a consistent approach to quality management in the manufacturing industry. As the concept of quality management gained traction worldwide, the International Organization for Standardization (ISO) recognized the importance of creating a global standard that could be applied across various industries and organizations. In 1987, ISO published the first edition of the ISO 9000 series, which included ISO 9001, ISO 9002, and ISO 9003, each addressing different aspects of quality management.
Since its initial release, ISO 9001 has undergone several revisions to ensure that it remains relevant and adaptable to the ever-changing business environment. The first significant revision took place in 1994, with an increased focus on quality assurance and a preventive approach to quality management. In 2000, ISO introduced a major overhaul of the standard, shifting the emphasis from quality assurance to a comprehensive Quality Management System (QMS) and incorporating the eight quality management principles that guided the standard until the 2015 revision.
ISO 9001:2008 brought minor adjustments and clarifications, but the most recent version, ISO 9001:2015, introduced a significant change by incorporating risk-based thinking and the High-Level Structure (HLS), which aligns the standard with other ISO management system standards. This update allows for more accessible integration of various management systems within an organization, streamlining processes and promoting a holistic approach to quality management. Through its evolution, ISO 9001 has become the most widely recognized and implemented QMS standard globally, helping organizations across industries to achieve operational excellence and customer satisfaction.
What Are Some Benefits of Being ISO 9001 Certified?
ISO 9001 certification offers numerous benefits to businesses seeking to improve their operations and establish themselves as leaders in their respective industries. First and foremost, obtaining this certification demonstrates a company’s commitment to maintaining a robust Quality Management System (QMS). By adhering to the globally recognized ISO 9001 standards, businesses can streamline their processes, reduce waste, and optimize their overall efficiency. This allows them to better manage their resources and consistently deliver high-quality products and services to their customers.
Another significant advantage of being ISO 9001 certified is the enhanced reputation and marketability it affords businesses. Clients and partners increasingly value organizations that prioritize quality and maintain internationally recognized certifications. As a result, ISO 9001 certified companies often enjoy increased credibility, which can lead to new business opportunities, better customer retention, and stronger relationships with suppliers and stakeholders. In addition, certification can serve as a valuable selling point for companies looking to differentiate themselves from their competitors and appeal to a wider audience.
Lastly, ISO 9001 certification can significantly contribute to a company’s continuous improvement efforts. By regularly reviewing and updating their QMS, certified organizations can identify areas for improvement, uncover inefficiencies, and address any issues that may arise. This ongoing process ensures that businesses remain adaptable and agile, better positioning them for long-term success. Furthermore, the systematic approach to management outlined by ISO 9001 promotes a culture of excellence and accountability within the organization. This helps to foster a positive work environment, in which employees feel motivated to take ownership of their tasks and strive for continuous improvement, leading to overall organizational growth and prosperity.
How much does it cost to get certified in Australia?
The cost of obtaining ISO 9001 certification in Australia can vary significantly depending on various factors, such as the size and complexity of your organization, the current state of your Quality Management System (QMS), and the level of support you require during the implementation process.
Generally, the overall cost can be broken down into two main components:
- The cost of preparing your organization for certification and
- The cost of the certification process itself.
The preparation costs include expenses related to training, consulting, and any internal resources required to develop and implement the QMS. Smaller organizations with simple processes may find that their preparation costs are relatively low, as they can quickly adapt to the ISO 9001 requirements. On the other hand, larger organizations or those with more complex operations may need to invest more time and resources to ensure full compliance with the standard, resulting in higher preparation costs.
Similarly, if you choose to engage the services of a consultant, this will add to the overall expense, though it may expedite the process and increase the likelihood of a successful outcome. The certification process costs include the fees charged by the Certification Body (CB) for conducting the initial certification audit, as well as any subsequent surveillance audits and recertification audits. These fees can vary depending on the CB, the size of your organization, and the complexity of your operations.
It is essential to view the investment in ISO 9001 certification as a long-term strategic decision that can bring numerous benefits to your organization, such as improved efficiency, increased customer satisfaction, and enhanced marketability. While the upfront costs may seem significant, the long-term value of maintaining a robust QMS aligned with the ISO 9001 standard can significantly outweigh the initial investment, leading to overall organizational growth and success.
How Can I get Certified?
Obtaining ISO 9001 certification in Australia involves a structured and methodical process that ensures your organization’s Quality Management System (QMS) meets the internationally recognized standards. The first step is to familiarize yourself with the requirements and principles of the ISO 9001 standard. It is essential to gain a thorough understanding of the standard’s core components, such as customer focus, leadership, risk management, and continuous improvement. Many organizations choose to engage the services of an experienced consultant to guide them through this process, while others opt for in-house training or online resources to build their knowledge base.
The next phase in the certification process involves conducting a gap analysis of your current QMS against the ISO 9001 requirements. This assessment will help you identify areas that require improvement or modification to comply with the standard. Once you have a clear understanding of the gaps, develop an implementation plan that outlines the necessary changes and assigns responsibilities for each task.
It is crucial to involve all relevant stakeholders, including management and staff, during this stage to ensure a successful implementation. As you execute the plan, consider conducting regular reviews and internal audits to monitor progress and address any issues that may arise. This will help your organization establish a culture of continuous improvement and demonstrate your commitment to quality management.
Upon completing the implementation of your QMS and ensuring it is aligned with the ISO 9001 requirements, it is time to engage the services of a Certification Body (CB) accredited by the Joint Accreditation System of Australia and New Zealand (JAS-ANZ) to conduct an external audit. The auditor will assess your QMS and verify its compliance with the ISO 9001 standard. If your organization successfully passes the audit, the CB will issue an ISO 9001 certificate, which is valid for three years. To maintain your certification, you will need to undergo regular surveillance audits by the CB to ensure your QMS remains compliant and continues to evolve with your organization’s needs and objectives.
Achieve Business Efficiency and Sustainable Growth
Don't let inefficient processes and outdated systems hold back your organization's growth! Experience firsthand how our fully featured operation management software can revolutionize the way you manage your business.
Seamlessly aligned with ISO 9001 standards, theBOSSapp offers a comprehensive project management system, staff matrix and training records, invoicing, purchase and contract tracking, controlled documents, and on-site digital dockets for clients.
Eliminate common pain points such as time-consuming mistake fixes and outdated systems. By embracing our cutting-edge operation management software, you can modernize your processes, streamline your workflow, and set the stage for long-term success.
Request a demo of theBOSSapp today and embark on the path to improved efficiency, customer satisfaction, and sustainable growth for your business.
Our Latest Articles
The Advantages of Digital Dockets: Ensuring Quality, Transparency, and Future Reference
Explore the numerous benefits of using digital dockets in the construction industry, including clear records of work, dispute prevention, and as a valuable reference for future projects.